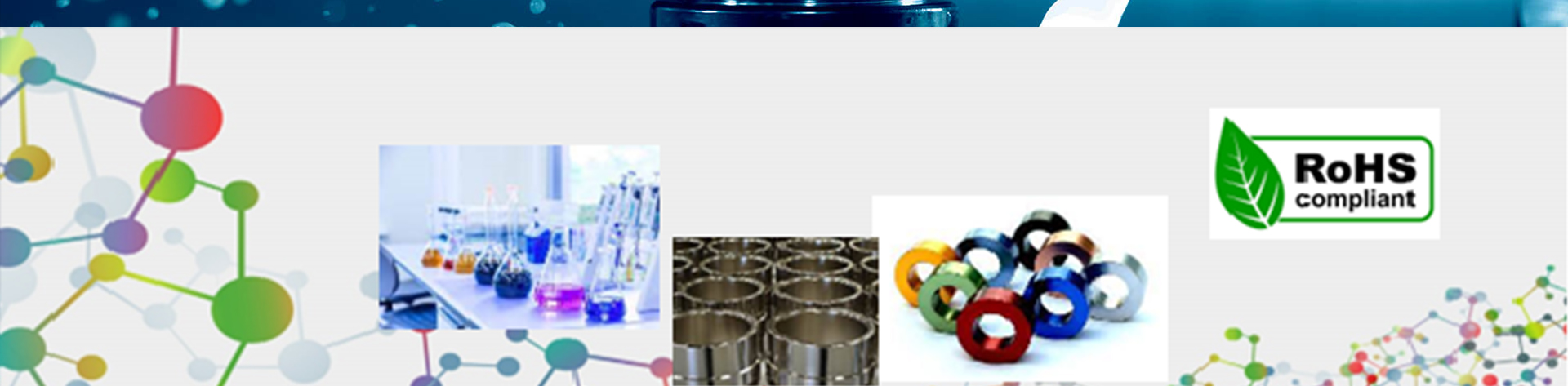
Equipment
Equipment. Modern CNC Machines.
Modern CNC machines are high-performance aggregates which are used in metal processing to manufacture both individual, complex parts as well as serial batches of typical parts. The machine is chosen according to the demands of part processing.
CNC milling services are widely used in the metalworking and in the woodworking industries. Experienced operator is one of the key aspects on the way of manufacturing of the high quality parts on CNC machines.
APRO is where you can find a wide range of professional equipment for metal processing and a team of experienced engineers and machine operators.
Okuma
The lathe Okuma IS-L8 II M is the intermediate model of the family Okuma-Echo Series. The others models are IS-L6 and IS-L10. This model has a version with motorised turret milling machines of 12 positions. The maximum diameter of cutting that reaches is of 210 mm and the maximum length of cut is 500 mm. The route of the axles is of 155 mm for the X and 520 for the Z. The turret milling machines has 12 positions. The speed of the cabezal of the husillo left is of 4.200 rpm and the one of the fast positioning is of 20 m/min for the axis X and of 25 m/min for the And. It goes instrumented with the control OSP-Or10L.
Mitsubishi Electric
Okuma OSP-U100L
MORI SEIKI
Mori Seiki CL2000B
8″ Kitagawa Chuck used mainly for secondary operations fitted with a Fanuc M10ia Robot Cell center for unattended operations.
DMG MORI
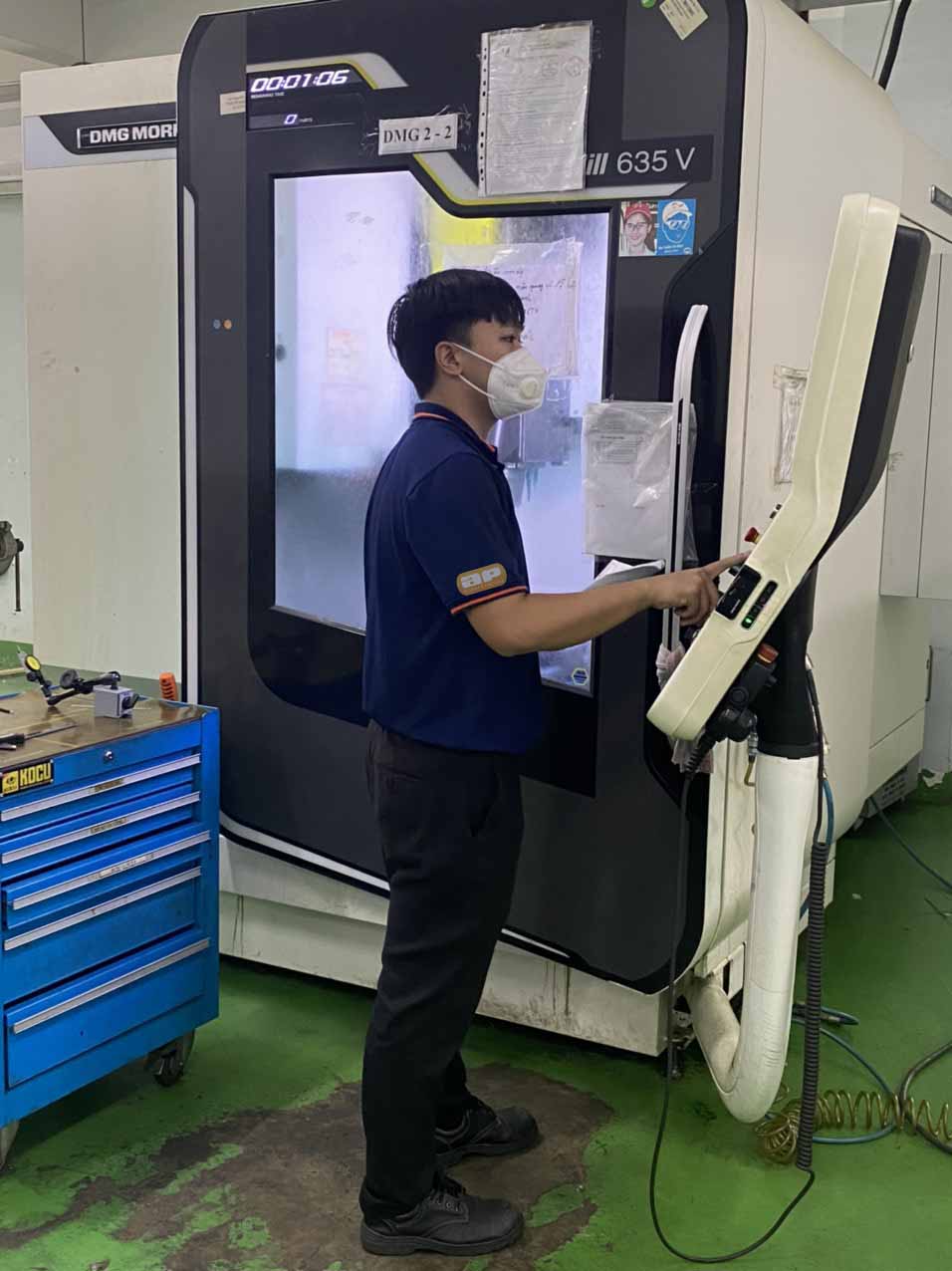
Makino SNC 43
NAKAMURA
Rockwell Hardness Tester
Mitutoyo Gauge
CMM Mitutoyo
2D Projector
Constructive elements of CNC machines
In its design, CNC machines are presented in the form of high-tech aggregate that are programmed for the implementation of specific operations.
Directional aggregates are characterized by high durability and provide precision of movements. The drive of the main movement in each CNC machine is able to cope with the high overloads and has a shiftless speed controller. Asynchronous motors are the most commonly used as drives. That guarantees precise and reliable performance of the equipment.
Feeder is one of the main elements of every CNC machine. It is the feeder that determines the overall tolerance of the processing part. Due to the low weight of acceleration, smooth running, slight frictional force and high stiffness of the kinematic chains, accurate data is obtained. Valve motors along with brake and feedback sensors are used as a drive.
The spindle of CNC machine provides the maximum accuracy of rotation, high wear resistance of the base surfaces and excellent rigidity. Efficient and smooth performance of the equipment element is achieved thanks to the inbuilt automatic devices and the heat dissipation systems.
CNC Machines. Classification
CNC turning machines are high-performance aggregates which are designed for external and internal metal cutting by means of rotation. Rotation serves as the main functional in the CNC turning processing, while the movement of the cutting tool is a translational motion.
CNC lathes are used for processing billets with a curved or multi-stage surface. Such feature makes CNC turning equipment one of the most commonly used aggregates for metal processing.
One of the peculiarities of CNC turning machines is their multifunctionality. That allows to process large batches of the parts in the shortest lead time possible. Such complex of technological operations as thread cutting, drilling, boring of conical, cylindrical or shaped surfaces etc., can be performed on CNC lathes. Fast processing of complex parts at the highest possible speeds is achieved with help of the system with tools for thread cutting.
In their structure, lathes are presented in the form of a unit with two controlled coordinates. The coordinate Z is responsible for the movement of the carriage along the spindle axis and the coordinate X ensures the movement of the sled. Each guide is fitted with a rotary head, the axis of which, depending on the model of the machine, can be located perpendicularly or parallel to the spindle axis. The high speed of metal processing is achieved due to the revolving heads. Tools for the simultaneous external and internal processing of the part are located on the revolving heads. As a result, a lot of time can be saved processing metal on CNC machines. CNC lathes with a large range of tools are used to process hard metals.
Turning processing of non-ferrous metals allows mass and smooth production of parts and billets of any structural complexity. The technology of turning processing is widely used in such fields of activity as machine building, automotive, energy, gas and oil and other industries.
CNC Milling Machines
Milling processing of metal on CNC machines is a complex process which results in the obtaining of parts with perfect geometry of the surface. Such operations as grinding of the surface or processing of shaped and simple surfaces may be performed on CNC milling machines. Milling processing of metal allows solving the problem of manufacturing of complex parts which can be used for various purposes.
The main task of milling on a CNC machine is to manufacture the perfect part of any structural complexity. Parts with unique shapes and surfaces can be easily processed on CNC milling machines due to their high precision. Moreover, such machines allow the processing of both small and large batches. Due to the individual programming of the machine, it can easily manufacture the part according to drawing’s requirement.
One of the benefits of the CNC milling machine is that such equipment can not only cut the metal and process different surfaces but also it can process various bulky structures. CNC milling of the metal will not result in melting, burning or unpleasant odor. That is more than important for the processing of visual objects.